内孔抛光:提升工业加工精度与效率的关键技术
内孔抛光技术的应用与意义
在现代工业加工中,内孔抛光技术作为一种高效的表面处理工艺,已经广泛应用于各类零部件的生产过程中,尤其是在航空、汽车、机械等行业中,它对提高零件的精度和性能起到了至关重要的作用。
1.什么是内孔抛光?
内孔抛光,顾名思义,就是对机械零件内部孔洞的表面进行细致打磨和抛光处理。这一技术主要通过精密的机械设备和专用的抛光工具,将零件内孔的粗糙表面抛光至平滑光洁,从而减少表面不规则性和提高表面光洁度。
抛光过程中,细微的磨料颗粒会与零件的内孔表面发生摩擦,去除表面的小瑕疵、氧化层和杂质,使得内孔表面更加平滑、光亮,并有效改善其耐磨性和耐腐蚀性。通过这一工艺处理后的零件,能够减少内孔部位的摩擦阻力,降低机器运转时的能量损耗,从而提高机械的整体运行效率。
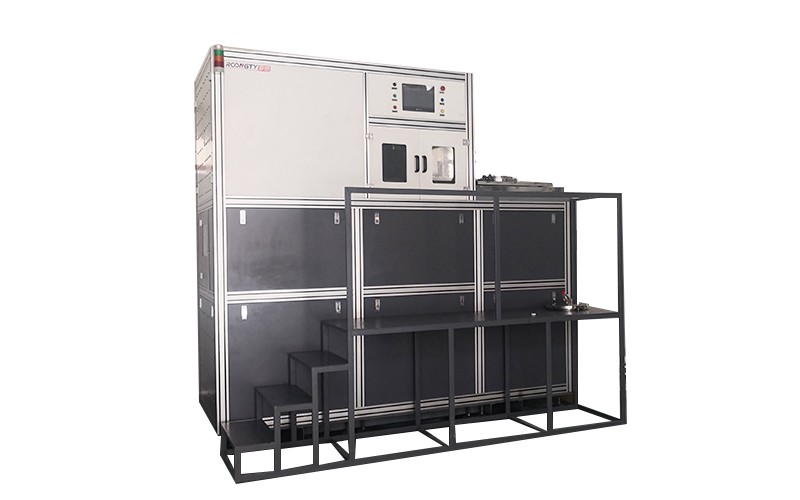
2.内孔抛光在工业中的应用
内孔抛光技术在许多行业中得到了广泛应用,尤其是在一些高精度、高要求的制造领域。例如,在汽车行业,发动机内部的各类零件,如气缸、活塞环、轴承等,都需要通过内孔抛光来提升其精度和表面质量,以保证发动机的平稳运行。而在航空航天领域,飞机发动机的精密部件、燃料喷嘴、导管等同样依赖于内孔抛光技术,保证了其在极端环境下的高效运转和长时间的可靠性。
内孔抛光也在医疗器械、精密仪器、液压系统等领域中发挥着重要作用。这些设备中的许多零件都需要经过内孔抛光,以保证其长期稳定的运行状态,减少故障发生率,提高设备的使用寿命。
3.内孔抛光的优势
内孔抛光不仅能够显著提高零件的表面质量,还能够有效提高零部件的使用寿命。抛光能够消除零件内孔表面的毛刺和不规则性,减少摩擦系数,从而降低机械运作中的能量损耗,提升加工精度。抛光后的内孔表面光滑,减少了物质的堆积和氧化,能有效延缓零件的磨损和腐蚀,使其更耐用,具有更长的使用寿命。
与此内孔抛光还能够提高加工效率。通过内孔抛光的精细加工,能够减少因表面不平整带来的加工误差,提高零部件的配合精度,从而降低后续加工过程中的修正工作量。对于复杂的机械设备,内孔抛光能够有效提升其整体性能,降低维修频率,减少运维成本。
4.内孔抛光的技术挑战
尽管内孔抛光技术在工业中具有广泛应用和显著优势,但其工艺的实现仍面临诸多挑战。例如,对于一些细长、深孔等难以接触的部位,如何保证抛光效果和均匀性成为技术难题。抛光过程中的设备选择、磨料的选用以及加工参数的调节也对最终效果有着极大的影响。如何精确控制这些变量,以实现最佳的抛光效果,仍是业内研究的重点。
内孔抛光的工艺优化与未来发展
随着技术的不断进步,内孔抛光工艺也在不断优化。现如今,越来越多的高效、环保的抛光技术被引入到工业生产中,极大地提高了加工精度和效率。未来,内孔抛光技术将在多个领域继续发挥其重要作用,并推动相关产业的升级与发展。
1.内孔抛光的工艺优化
为了提高内孔抛光的精度与效率,许多先进的技术已经被应用于实际生产中。例如,超声波抛光技术就是一种利用高频振动的方式对内孔进行精细处理的方法。该技术能够有效去除表面微小的缺陷,使得内孔表面更加光滑,而且不易产生热变形,适用于要求较高的精密加工。
数控技术的应用也为内孔抛光提供了更高的自动化水平。通过精确的数控系统,抛光过程中的每一个步骤都可以在精确控制下完成,大大减少了人为误差,提高了加工的稳定性与重复性。数控内孔抛光机的使用,不仅提高了加工效率,还降低了生产成本。
2.环保与可持续发展的抛光工艺
随着环保意识的提高,传统的抛光工艺正在朝着更加绿色、环保的方向发展。传统抛光中使用的磨料和化学试剂常常会对环境造成污染,因此,许多企业正在研究无污染、无毒的环保抛光材料,以及减少化学品使用的清洁工艺。抛光设备也在向节能和高效方向发展,减少能源消耗的提高加工效率。
3.内孔抛光技术的未来前景
随着自动化、智能化技术的发展,未来内孔抛光技术将越来越趋向于智能化和精细化。通过集成先进的传感技术、数据采集系统和人工智能算法,抛光过程可以实现更加精确的控制,自动调节加工参数,确保零件表面质量的稳定性和一致性。
未来,内孔抛光将不仅仅局限于机械加工领域,还将扩展到更多领域,如新能源、电子、精密医疗设备等。随着对加工精度要求的提高,内孔抛光技术将继续引领行业发展,并成为制造业高效、精密加工不可或缺的一部分。
内孔抛光作为提升零部件表面质量和性能的关键技术,在现代工业生产中扮演着重要角色。随着技术的不断革新,内孔抛光将在更多领域发挥更大的价值,推动整个制造行业向着更高效、更环保、更智能的方向迈进。