去毛刺,让产品更完美——精益求精的工艺之道
在现代制造业中,产品的质量是企业能否获得市场认可的关键因素之一。而在整个生产过程中,去毛刺工艺的应用,作为提升产品精度和外观的关键环节,已经逐渐成为了制造业的标配技术。去毛刺不仅仅是为了产品的美观性,更是从根本上提高了产品的安全性和使用寿命。在这篇文章中,我们将深入探讨去毛刺的重要性、去毛刺的不同方式,以及其在各个行业中的应用和价值。
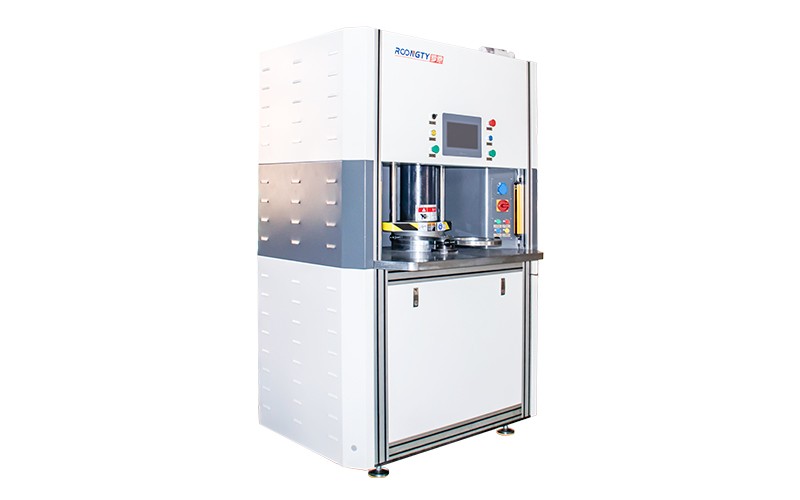
让我们了解一下什么是去毛刺。简单来说,去毛刺就是将金属、塑料、铝合金等材料在加工过程中产生的毛刺、锐边和不平整部分去除的过程。毛刺是一种在切割、冲压、铣削等加工过程中不可避免的现象。毛刺的存在,不仅影响产品的外观,甚至会引发安全隐患,例如刺伤人体、损坏产品结构等。对于一些精密设备来说,毛刺还可能影响设备的正常工作,因此去毛刺在生产过程中尤为重要。
去毛刺不仅是一项技术工作,它更是提升产品整体质量的重要保障。去毛刺能够有效地避免产品在使用过程中因为毛刺带来的安全隐患,尤其是在一些高精度、高性能的行业,毛刺可能会影响产品的使用寿命,甚至引起故障。因此,通过去毛刺工艺,能够大大降低这些风险。去毛刺还可以提高产品的外观,去除毛刺后,产品表面更加平整光滑,给人以更加精致、优质的感觉,这对于提高品牌形象也有着重要的作用。
随着技术的不断发展,去毛刺的手段也在不断创新。从最早的手工去毛刺到如今的自动化、智能化去毛刺,技术的进步让去毛刺变得更加高效、精准和环保。例如,现代化的去毛刺设备能够根据产品的材质、形状、大小等因素,自动调整工作参数,以达到最佳的去毛刺效果。使用先进的去毛刺工具和技术,不仅可以提高生产效率,还能确保每一件产品都能达到相同的高标准。
去毛刺的应用领域非常广泛,几乎涵盖了各个行业。在汽车制造、航空航天、电子产品、家电以及医疗器械等行业中,去毛刺都是确保产品质量、提升产品性能的关键步骤。在汽车行业,去毛刺能够有效避免车辆零部件在运转过程中因为毛刺导致的摩擦损坏,从而延长汽车的使用寿命。在航空航天领域,去毛刺不仅仅是为了美观,更关乎飞行安全,因为任何微小的瑕疵都有可能在高压、极端温度等环境下引发故障。
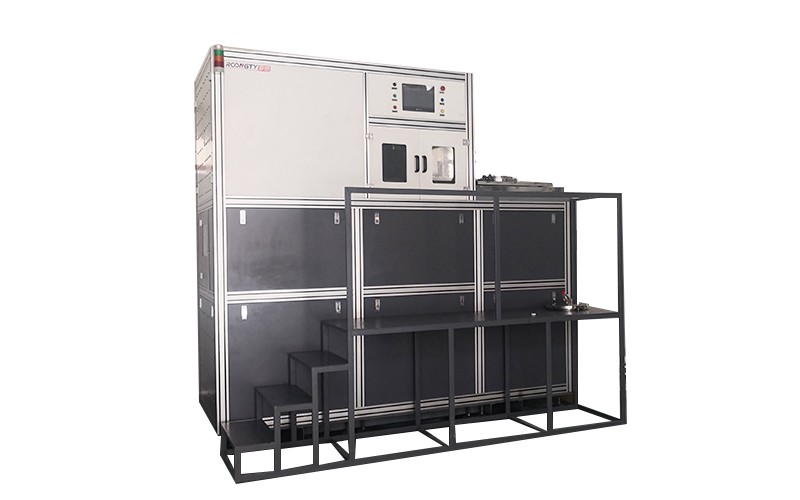
随着市场对高品质产品的需求不断增加,去毛刺的技术也逐渐从单一的物理去毛刺发展为多样化的综合处理方案。目前,常见的去毛刺方式包括手工去毛刺、机械去毛刺、化学去毛刺和电解去毛刺等。每种方法都有其独特的优缺点,企业可以根据具体的生产需求,选择合适的去毛刺技术。
手工去毛刺是最传统的去毛刺方法,通常用于一些小批量生产或者需要高精度的产品。它需要工人使用手动工具,如砂纸、磨刀石等,将毛刺手工打磨去除。这种方法的优点是操作简单,适合处理复杂的产品,但生产效率较低,且人工操作难以保证一致性。
机械去毛刺则使用专门的去毛刺机器,通过机械力将毛刺去除。常见的机械去毛刺方法包括振动去毛刺、喷砂去毛刺、滚轮去毛刺等。这些方法能够大大提高生产效率,并且具有较高的一致性和稳定性。特别是对于大批量生产的企业来说,机械去毛刺是提高生产效率、降低成本的有效手段。
化学去毛刺是一种通过化学反应去除毛刺的方法。它主要通过使用酸性溶液来溶解毛刺,从而实现去毛刺的目的。化学去毛刺的优势在于它可以对复杂形状的产品进行精细处理,但其缺点是需要对溶液进行特殊处理,且化学药剂可能对环境造成一定影响,因此在应用时需要特别注意环保问题。
电解去毛刺是利用电解作用去除毛刺的一种方法。它通过在电解液中施加电流,使毛刺部分与基体金属发生电化学反应,从而去除毛刺。这种方法具有较高的精度,可以去除细小的毛刺,并且不会对产品造成损伤。电解去毛刺适用于一些高精度、高要求的产品,尤其是在电子、航空等高端行业中得到了广泛应用。
除了技术手段的不断进步,去毛刺设备的智能化也是一个重要趋势。如今,许多去毛刺设备已经配备了智能控制系统,能够根据不同产品的加工要求,自动调整工作参数,实时监控加工过程,确保每一件产品都符合标准。这不仅提高了生产效率,还有效减少了人为操作失误,进一步保证了产品的质量和一致性。
总结来说,去毛刺工艺已经成为现代制造业中不可或缺的一部分。通过不断创新和优化,去毛刺不仅能够提升产品的外观和质量,还能够确保生产安全,降低故障率。在未来,随着制造技术的不断进步,去毛刺将继续发挥其重要作用,成为推动企业提升竞争力、实现持续发展的关键因素之一。