磨料流去毛刺:打造完美工件表面,提升加工效率
磨料流去毛刺技术:提高工件表面质量的新选择
随着制造业的不断发展,产品质量和生产效率的提升已成为企业核心竞争力的关键。而在机械加工过程中,去除毛刺是一个不可忽视的重要步骤。毛刺不仅影响工件的外观和表面质量,还可能对后续加工造成影响,甚至影响最终产品的使用性能。如何有效、快速且精确地去除工件毛刺,成为了众多企业需要解决的难题。
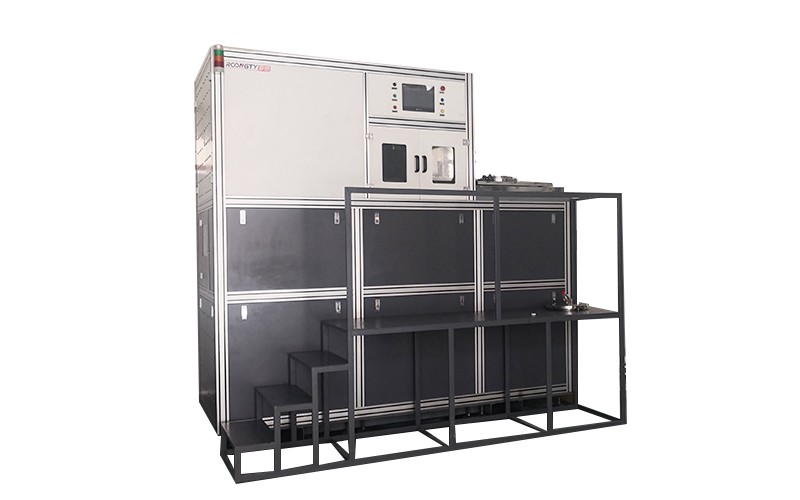
近年来,磨料流去毛刺技术(AbrasiveFlowMachining,AFM)以其独特的优势,成为了一种广泛应用于各类工件表面处理的技术手段。磨料流技术是一种通过流动的磨料浆液对工件表面进行抛光和去毛刺的非传统加工方法。其工作原理是在工件表面通过流动的磨料介质对毛刺进行物理磨削,从而达到去除毛刺、平滑表面的目的。
一、磨料流去毛刺技术的工作原理
磨料流去毛刺的核心在于磨料介质的流动。在加工过程中,磨料浆液由高压泵通过管道进入特定的加工腔体。工件被放置在加工腔体中,磨料浆液高速流动,通过磨料与工件表面发生摩擦,去除表面多余的毛刺。此过程类似于一种流体磨削,通过在工件表面施加均匀的磨削力,实现去毛刺的目的。
磨料流去毛刺技术的最大优势之一是其能够对复杂形状的工件进行均匀的表面处理。与传统的机械去毛刺方法相比,磨料流技术可以处理多种形状的工件,甚至是内孔、细小沟槽等复杂部位,确保所有部位的毛刺都能被彻底清除。
二、磨料流技术的应用领域
磨料流去毛刺技术广泛应用于航空、汽车、电子、医疗、精密机械等多个行业。在航空航天领域,许多高精度的航空部件要求表面没有任何毛刺和瑕疵,以保证其在极端条件下的性能。在汽车行业,发动机零件、涡轮增压器等部件的表面处理需要非常精细,磨料流去毛刺技术能够帮助去除微小毛刺,从而提高零件的质量和性能。在电子行业,微型元器件的表面精度要求也非常高,磨料流技术凭借其精细的加工能力,成为了这些高精度加工的理想选择。
随着制造工艺的进步,医疗器械、精密机械等领域也逐渐开始应用磨料流技术,用于去除金属表面或塑料表面的微小毛刺,确保最终产品的精密度与安全性。
磨料流去毛刺技术的优势与设备选择
三、磨料流去毛刺的优势
磨料流去毛刺技术相比传统的机械去毛刺方法,具有诸多显著的优势:
高效且均匀:磨料流技术能够在短时间内完成去毛刺处理,且加工效果均匀,不会对工件表面造成过度磨损或损伤,适用于大批量生产。
适应复杂形状:由于其可以对工件的内外表面进行全方位的处理,无论是复杂的几何形状、微小的细节部位,还是难以触及的内孔,都能够轻松处理,确保每个角落都不留毛刺。
无接触式加工:磨料流去毛刺技术采用液体磨料介质进行加工,与工件表面接触的仅仅是磨料液体,不会产生机械压力,因此避免了传统机械加工中因压力过大导致的形变或损伤。
环保:与传统的去毛刺方法相比,磨料流技术使用的磨料和液体可循环使用,减少了资源浪费,也避免了大量的粉尘、废料产生,从而更加环保。
四、如何选择合适的磨料流去毛刺设备
选择合适的磨料流去毛刺设备是确保加工效果的关键。设备的性能和工件的材料类型以及加工精度要求密切相关。对于高精度要求的部件,选择一台精密度高、流体控制系统稳定的设备非常重要。根据加工量的不同,企业可以选择不同规格的磨料流设备,自动化程度较高的设备能有效提高生产效率,减少人工干预。
磨料流去毛刺设备的维护和操作简单程度也需要考虑,优质的设备能够保证长期稳定运行,降低维修成本。企业在选择设备时应关注供应商提供的技术支持和售后服务,确保设备能够在长期使用中维持高效的加工效果。
五、结语
磨料流去毛刺技术作为一种高效、环保的表面处理方法,已经成为各类工业领域的重要技术手段。随着制造技术的不断进步,磨料流去毛刺将在更多行业中发挥重要作用,帮助企业提升加工质量、缩短生产周期、降低成本,从而增强市场竞争力。
通过选择合适的磨料流去毛刺设备,制造企业不仅能够提高产品质量,还能显著提升生产效率,走向更加智能化、自动化的未来。