金属加工去毛刺的重要性与解决方案
金属加工去毛刺:提升产品质量与生产效率的关键
在现代制造业中,金属加工去毛刺是一项不可忽视的关键工艺。无论是在航空航天、汽车制造、精密机械,还是电子产品的生产中,金属表面毛刺的去除都对最终产品的质量和性能至关重要。毛刺是金属零部件在切割、铣削、冲压、磨削等加工过程中产生的锋利边缘或凸起部分,它们不仅影响外观,更会对产品的性能、耐用性和安全性造成严重影响。
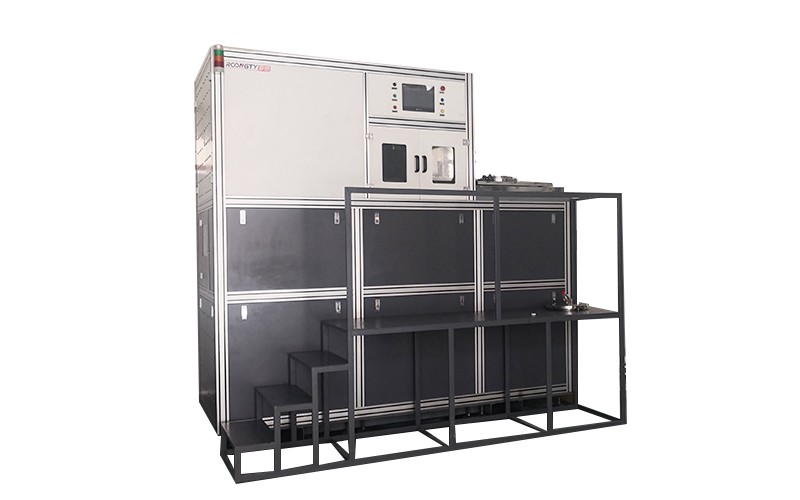
毛刺会影响零部件的装配精度。在机械装配过程中,毛刺可能导致零部件之间的配合不良,进而影响整个设备的稳定性与运行效果。例如,在汽车发动机的制造中,毛刺可能导致齿轮啮合不良,影响传动效率,甚至引发故障。因此,去除毛刺能够确保零部件能够精准配合,提升装配精度。
毛刺还会影响金属零部件的使用寿命。毛刺可能成为金属疲劳的起点,导致金属表面出现裂纹,从而缩短产品的使用寿命。在许多高要求的行业中,产品的使用寿命直接关系到企业的品牌声誉和经济效益。例如,航空航天领域的零部件要求极高的耐久性,任何微小的毛刺都可能引发灾难性的后果。因此,通过高效的去毛刺工艺可以有效避免这一问题,提高产品的可靠性和安全性。
除了对产品质量的影响外,毛刺还可能成为工人的安全隐患。锋利的毛刺在操作过程中容易割伤工作人员的手部或皮肤,造成不必要的工伤。因此,为了保障生产线的安全,去毛刺不仅是对产品质量的提升,也是对工人安全的保护。
在提高生产效率方面,去毛刺的工艺也发挥着重要作用。毛刺的存在不仅增加了后期的清理工作量,还可能影响后续加工过程的顺利进行。比如,在数控机床上加工零件时,毛刺可能干扰到下一道工序,造成生产效率的降低。通过精确的去毛刺工艺,可以有效降低二次加工的难度,加快生产周期,提升整体生产效率。
目前,随着工业技术的不断发展,去毛刺的解决方案也在不断创新。传统的去毛刺方法包括人工手工打磨、喷砂、磨光等,但这些方法往往耗时长、效率低,且易受到工人操作水平的限制。为了满足现代工业生产中对高效率、高质量的要求,越来越多的企业开始采用自动化去毛刺设备,如机械去毛刺机、振动去毛刺机、激光去毛刺等先进技术。这些新型技术不仅能够大幅提升去毛刺的效率,还能保证更高的精度,满足不同加工需求。
例如,机械去毛刺机通过高速旋转的砂轮、刀具或刷轮对金属表面进行处理,能够快速、均匀地去除毛刺。与人工手工去毛刺相比,机械去毛刺机的加工效率高,且避免了人为操作误差。自动化去毛刺设备的普及也降低了人工成本,提高了生产线的自动化程度,进一步提升了企业的竞争力。
金属加工去毛刺解决方案:从传统到现代的技术革新
随着制造业对产品精度要求的不断提升,金属加工去毛刺的技术也经历了多次革新。传统的手工打磨虽然操作简单,但其效率低、成本高,并且无法保证一致的去毛刺效果。因此,越来越多的企业选择采用先进的自动化去毛刺技术,以提高生产效率、保证产品质量。
振动去毛刺技术是一种常见的自动化去毛刺方法。它通过振动装置将工件与研磨介质一起在容器内进行振动,使工件表面的毛刺逐渐被磨去。这种方法适用于大批量生产,尤其是在处理形状复杂的零部件时,具有显著的优势。振动去毛刺的设备通常能够实现批量处理,并且可以精确控制去毛刺的深度和均匀性。与传统的手工去毛刺相比,振动去毛刺的效率大大提高,且对操作人员的技术要求较低。
激光去毛刺技术则是近年来随着激光技术的发展而出现的一种创新性解决方案。激光去毛刺利用激光束的高能量在金属表面进行精细加工,能够去除微小的毛刺,且不损伤工件的基体。激光去毛刺具有非接触性的优势,能够处理高精度、高难度的零部件,特别是在航空航天、精密仪器等领域得到了广泛应用。激光去毛刺不仅能够提高产品的精度,还能够节省大量的人工成本,是未来金属加工领域的一大趋势。
除了这些高效的机械方法外,化学去毛刺技术也逐渐在某些行业中得到应用。化学去毛刺通过化学溶液溶解金属表面的毛刺,适用于那些形状复杂、材料坚硬的零部件。这种方法通常被用于精密加工中的微小零部件,可以非常精确地去除毛刺,同时不损伤工件表面。化学去毛刺的操作需要严格控制化学品的浓度和温度,且有一定的环境污染问题,因此在一些环保要求较高的行业中应用较为有限。
尽管现代去毛刺技术不断更新换代,但传统的手工去毛刺和机械去毛刺设备仍然是许多小型企业和低批量生产中的常见选择。对于这些企业而言,成本效益和设备维护是主要考虑因素。因此,选择合适的去毛刺方法,不仅要根据产品的要求,还要结合企业的生产规模、技术水平和成本预算进行综合评估。
金属加工去毛刺是一项十分重要的工艺,不仅关系到产品的质量和安全性,也直接影响生产效率。在现代制造业中,随着技术的不断发展和创新,去毛刺的解决方案也在不断进步。从传统的手工打磨到高效的自动化设备,再到激光去毛刺等先进技术,企业在选择去毛刺方法时,需根据具体情况进行权衡,选择最适合的技术,以确保在提升产品质量的降低生产成本、提高生产效率。