毛刺定义与应用:让工业精度更上一层楼
好的,下面是您要求的软文,分为两部分。第一部分和第二部分分别各700字:
在金属加工领域,毛刺是一个无法忽视的问题。无论是钣金冲压、铣削、切割还是精密机械加工过程中,毛刺都可能悄然出现。毛刺的存在不仅影响产品外观,甚至可能影响产品的正常使用,造成设备故障或者安全隐患。因此,了解毛刺的定义及其处理方式,对于提升产品质量至关重要。
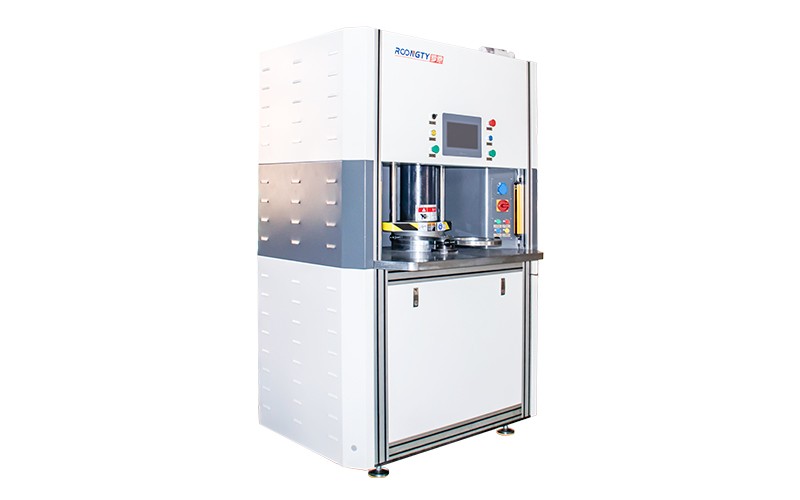
毛刺的定义
毛刺,顾名思义,就是金属加工件表面突起的细小碎屑或不规则物质。它通常在切割、冲压、铣削、磨削等机械加工过程中产生,属于不希望出现在产品表面的附加物。毛刺可能会出现在工件的任何边缘或孔洞周围,尤其是在锋利或快速切割时。毛刺的形态千变万化,可能是微小的、尖锐的,也可能是较大的、粗糙的,甚至呈现出不同的方向性。
虽然毛刺的出现几乎是每个机械加工过程中的副产品,但它却具有一定的危害性。如果不及时去除,不仅会影响产品的美观,还可能导致下游装配过程中产生误差,影响零件之间的配合精度,甚至导致设备的性能下降。
毛刺的产生原因
毛刺的产生原因主要与加工过程中产生的压力、温度及材料特性相关。以铣削为例,当刀具切入工件时,材料的表面会被切削下来,但由于切削力的作用,材料的边缘会被拉伸或挤压,从而形成突起的毛刺。而在冲压过程中,模具的剪切力也会对材料产生类似的效果,使其边缘出现不规则的毛刺。
不同的加工工艺和材料也会影响毛刺的产生程度。例如,硬度较高的材料比软质材料更容易在加工过程中产生较为坚硬的毛刺;而切削速度、进给量、刀具形状等加工参数也会直接影响毛刺的形态和数量。
毛刺的危害性
毛刺虽小,但它的危害不可忽视。毛刺会影响产品的装配精度,尤其是在精密机械装配中,毛刺会导致零件无法完美配合,从而影响整个设备的正常运转。毛刺的存在会影响产品的外观,给客户留下不专业的印象,影响企业的品牌形象。毛刺尖锐的部分可能会对操作者造成伤害,尤其是在金属加工企业的生产过程中,操作人员如果不小心接触到毛刺,极易割伤手部,带来安全隐患。
除了上述问题,毛刺在某些行业的特殊应用中,可能会直接影响产品的功能。例如,在汽车、航空航天等行业中,毛刺可能会干扰到部件的运动或连接,从而影响整个设备的运行效率或安全性。因此,在这些高精度要求的领域,去除毛刺显得尤为重要。
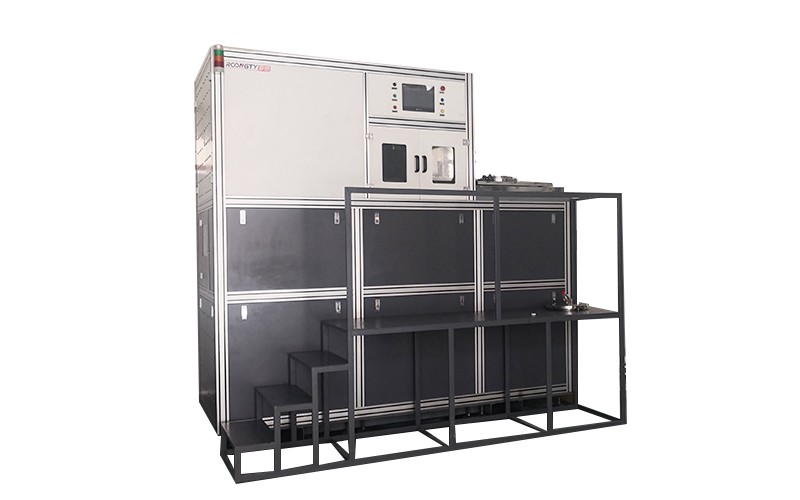
毛刺的去除方法
针对毛刺的去除方法,工业界已有多种技术和工艺。具体选择哪种去毛刺方式,通常取决于工件的材料、毛刺的形态以及生产要求。常见的去毛刺方法包括机械去毛刺、电解去毛刺、化学去毛刺以及激光去毛刺等。
机械去毛刺法
机械去毛刺法是目前应用最为广泛的一种方法,主要通过机械工具去除工件表面的毛刺。常见的设备有去毛刺机、振动去毛刺机、手持式去毛刺工具等。这些工具通过研磨、抛光、刮削等方式去除毛刺,操作简单且高效。适用于大部分材料的毛刺去除,但对于精密度要求较高的零件,可能需要额外的精细调整。
电解去毛刺法
电解去毛刺法是一种利用电化学反应的方式来去除毛刺的工艺。通过将工件浸入电解液中,并施加电流,使工件表面的毛刺部分发生溶解,达到去毛刺的效果。电解去毛刺具有较高的精度,适用于复杂形状或小尺寸的零件,但其成本较高,操作时需要注意电解液的配置和电流的调节。
化学去毛刺法
化学去毛刺法是通过化学溶液将工件表面的毛刺溶解掉的一种方法。这种方法适用于较为精密的工件,尤其是表面较光滑的零件。其优势在于可以实现较为均匀和细致的去毛刺效果,特别适合大批量生产。这种方法的缺点在于溶液的使用需要严格控制,且化学品的使用可能带来一定的环境问题。
激光去毛刺法
激光去毛刺法是近年来新兴的一种高效去毛刺技术,通过高能激光束照射工件表面,使毛刺迅速蒸发或熔化。该方法去毛刺效率高、精度高,特别适合高精度和复杂形状的零件,但设备投资较大,适用于高端制造业。
总结
毛刺的存在是工业生产中不可避免的一部分,但通过科学的管理和合理的技术手段,完全可以有效地去除毛刺,确保产品的质量和安全。了解毛刺的定义、产生原因以及去除方法,能够帮助企业在生产过程中实现更高的精度要求,提升产品的市场竞争力。
随着工业技术的不断进步,去毛刺技术也在不断创新和发展。企业应根据自身生产需求,选择合适的去毛刺方式,确保产品质量和生产效率的双重提升。在未来,毛刺处理技术将继续在工业制造中扮演重要角色,推动行业走向更高精度、更高效益的未来。