内孔镜面抛光工艺:提升精密制造的关键技术
在现代工业制造中,精密加工技术越来越成为推动生产效率和产品质量提升的核心动力。在众多精密加工技术中,内孔镜面抛光工艺以其出色的表面处理效果和广泛的应用前景,成为了众多行业中的核心技术之一。作为一种高精度加工工艺,内孔镜面抛光不仅提升了内孔表面的光洁度和精度,还有效改善了材料的性能,延长了产品的使用寿命。
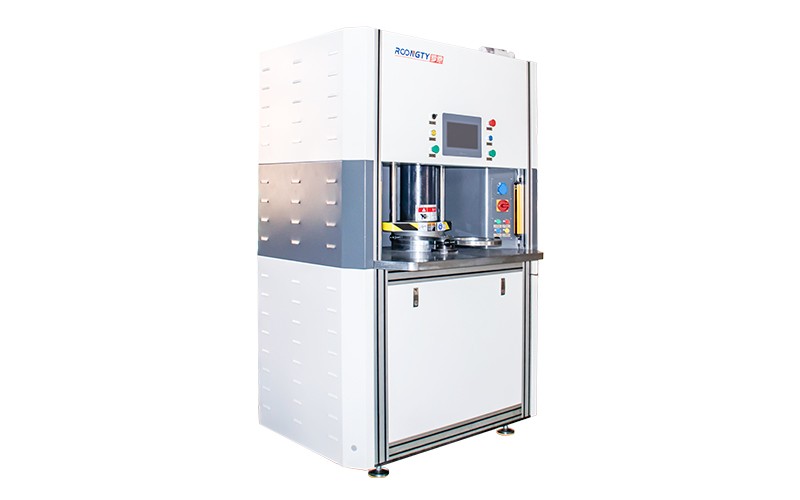
内孔镜面抛光工艺的主要目的是通过物理和化学方法对内孔表面进行精细处理,使其达到镜面般的光滑效果。这个过程不仅能够消除内孔表面的粗糙度和微小缺陷,还能改善孔内表面的平整度和光洁度。为了达到这一效果,通常会使用抛光液、抛光工具和先进的设备,结合适当的压力和速度进行多次精细操作。这一工艺的实施,能够大大减少摩擦阻力,降低能耗,并有效延长部件的使用周期。
特别是在航空航天、汽车制造、电子通讯、精密机械等领域,内孔镜面抛光工艺被广泛应用。以航空发动机的涡轮叶片为例,发动机内部的内孔需要极为光滑,以确保高效的气流通过。任何微小的表面粗糙度都可能导致气流的不稳定,进而影响发动机的性能和安全性。因此,内孔镜面抛光工艺在这些高要求的行业中不可或缺。
内孔镜面抛光技术的应用不仅仅是为了表面美观,更多的是为了提升性能。在机械领域,内孔的光洁度直接影响到零部件之间的配合精度和运行稳定性。例如,在液压系统中,内孔的光滑程度对液体流动的阻力有着至关重要的影响。光滑的内孔可以显著减少摩擦,降低能耗,提升系统效率。内孔表面平滑处理后,能够更好地抵抗腐蚀和磨损,从而有效延长零部件的使用寿命。
随着技术的不断进步,内孔镜面抛光工艺已经不仅仅依赖于传统的手工抛光。现代化的机械设备和数控系统使得这一工艺更加精准和高效。高精度的数控机床能够通过自动化控制,精确调节抛光参数,使得加工效果更加一致。抛光过程中使用的抛光液也在不断改进,加入了更多高效的添加剂,使得抛光效果更加显著,且对环境的影响降到了最低。
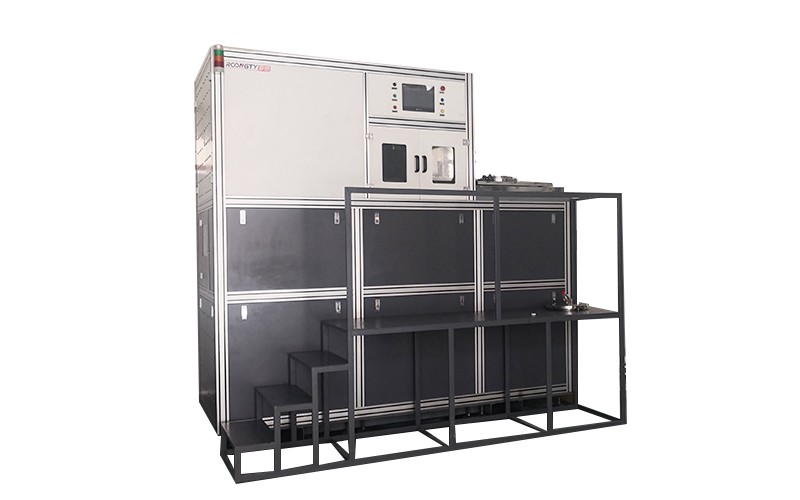
这种技术的创新使得内孔镜面抛光工艺在更多行业中得到应用。例如,在医疗器械领域,许多高精度的医疗设备,如内窥镜、手术工具等,都需要具备极高的表面光洁度。通过内孔镜面抛光工艺,可以有效地提升这些设备的性能,降低术中感染的风险,提高病人的治疗效果。
内孔镜面抛光工艺也面临一些挑战。由于内孔形状的复杂性,抛光过程中的精度控制要求极高,任何细微的误差都可能影响到最终产品的质量。工艺过程中需要使用高精度的抛光设备和工具,这不仅要求技术人员具备丰富的经验,还需要不断进行设备和工具的升级和创新。因此,如何在保证高质量的前提下,降低生产成本,提高效率,仍然是业内技术人员需要攻克的难题。
除了提升产品质量和性能外,内孔镜面抛光工艺的另一个重要优势是其环保性。随着环保意识的不断提升,越来越多的制造企业开始重视生产过程中对环境的影响。传统的抛光方法常常会产生大量的废料和污染物,而现代内孔镜面抛光工艺则通过更加精细的控制和优化,大大减少了废料的产生,并且使用的抛光液和工具对环境的影响也得到了有效降低。这不仅符合绿色生产的理念,也符合国家对企业环保的相关要求。
内孔镜面抛光工艺的不断发展和创新,也推动了整个精密制造行业的技术进步。如今,许多企业通过研发更高效的抛光工具和设备,突破了技术瓶颈,提升了生产效率。这些创新不仅降低了生产成本,还提升了产品的市场竞争力。可以预见,随着科技的不断进步,内孔镜面抛光工艺将会在更多行业中得到广泛应用,并为行业的发展提供强大的技术支持。
对于企业来说,投资内孔镜面抛光工艺的应用,不仅能提升产品的质量,还能增强企业的技术实力和市场竞争力。精密制造的未来将离不开内孔镜面抛光工艺的支持,而这种工艺的不断优化和发展,将为企业带来更多的机遇。
内孔镜面抛光工艺作为精密制造中的核心技术,不仅能够提升产品的性能和寿命,还能推动行业技术的进步。无论是在航空航天、汽车、机械制造还是医疗器械等领域,这项技术都具有重要的应用价值。未来,随着技术的不断创新,内孔镜面抛光工艺将在更多领域发挥重要作用,成为推动产业升级的重要力量。