什么是毛刺?揭秘毛刺的成因与危害
什么是毛刺?
在日常生活中,我们经常听到“毛刺”这一词汇,尤其是在谈论机械加工或金属制造时,毛刺几乎是无法避免的一种现象。究竟什么是毛刺呢?毛刺是指在金属加工过程中,工件的边缘或表面由于切削、打磨、冲压等工艺操作所产生的细小凸起物或者金属碎屑。它们通常是由于工具的磨损、加工不当或工艺参数设置不当所导致的。
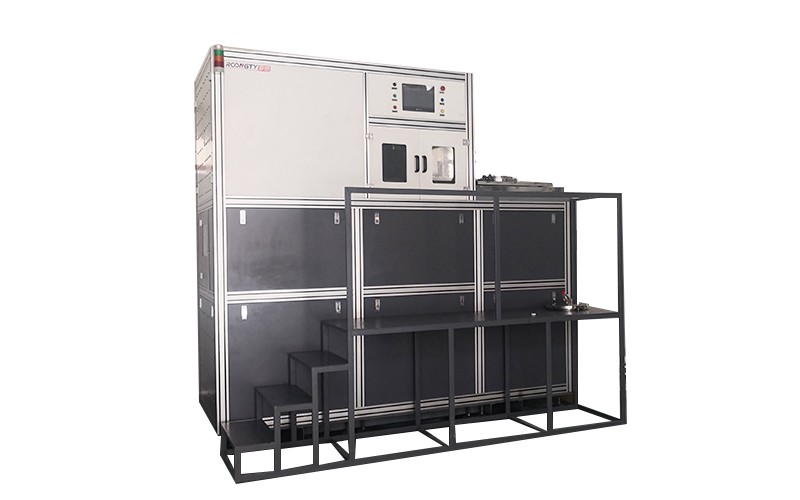
毛刺看似不显眼,但其影响却十分严重。它不仅影响工件的外观,还会对后续的加工、装配甚至使用造成障碍。可以说,毛刺是金属加工中的“隐形杀手”,它不仅影响生产效率,甚至可能导致机械故障和设备损坏。
毛刺的产生过程
毛刺的产生与机械加工中的许多因素密切相关。常见的导致毛刺的加工方式有切割、铣削、钻孔、冲压等。在这些工艺过程中,工件的边缘容易由于工具的切削作用而变形或断裂,形成小小的突起物。尤其在金属表面,受力不均匀或者刀具角度不合适时,毛刺的生成几率更高。
例如,在冲压工艺中,模具和工件之间的摩擦力可能导致工件边缘的微小裂纹扩展,这些裂纹会迅速形成毛刺。而在铣削或车削过程中,刀具的尖端与工件之间的摩擦力也会导致金属表面产生微小的凸起。这些凸起物一旦不被去除,便会影响产品的质量,甚至可能导致装配不良、机械故障等问题。
毛刺的种类
根据毛刺的形态和大小,毛刺可以分为几种不同的类型:
飞边型毛刺:这种毛刺通常在冲压或者剪切过程中出现,边缘较为光滑,形状不规则,通常以锋利的金属边缘呈现,容易刮伤人或损坏其他零部件。
裂纹型毛刺:在铣削或车削过程中,由于切削力的不均匀或刀具磨损不当,工件的边缘常会形成裂纹,这些裂纹沿着金属表面扩展并逐渐形成毛刺。裂纹型毛刺一般较为细小,但十分锋利。
拉毛型毛刺:这种毛刺通常出现在铣削或车削过程中,金属表面被拉伸形成细长的凸起物。拉毛型毛刺的形态较为规整,容易通过一定的加工去除。
厚重型毛刺:此类毛刺通常较为粗大,通常出现在切割过程中,常见于金属加工的初期阶段,通常需要经过后期处理才能去除。
不同类型的毛刺所带来的危害各不相同,因此,对于不同类型的毛刺,需要采取不同的处理方式。
毛刺的危害
虽然毛刺看似微不足道,但它带来的危害却远比我们想象的要大。毛刺的存在不仅影响工件的外观,更可能直接影响到产品的功能性和安全性。以下是毛刺的几大危害:
影响产品外观:毛刺会使得金属工件表面不平整,影响其美观度。在一些要求高质量外观的产品中,毛刺往往成为影响产品质量的一个重要因素。
影响装配精度:在精密机械装配中,毛刺往往会影响零部件之间的配合精度。毛刺可能导致零部件间的间隙不符合标准,从而影响整机的正常运转。
降低使用寿命:机械部件如果存在毛刺,可能会导致摩擦增加,磨损加剧,从而缩短设备的使用寿命。尤其是在高负荷、高速运转的机械中,毛刺的存在可能导致故障和损坏。
安全隐患:毛刺的锋利边缘可能会伤及工人,特别是在工业生产中,如果工件表面带有毛刺,操作人员在搬运、安装或维修过程中容易发生割伤事故。
影响后续加工:毛刺如果未被去除,可能会在后续加工过程中干扰工件的进一步处理。例如,毛刺可能导致涂层不均匀,或者在焊接过程中出现不良接触,影响焊接质量。
增加生产成本:毛刺的存在往往意味着需要额外的去除和处理工序,这不仅增加了工时,还可能带来额外的设备和材料消耗,导致生产成本上升。
在了解了毛刺的成因和危害后,企业和生产厂家应采取积极的措施来控制毛刺的产生,确保产品质量。
如何去除毛刺及预防措施
针对毛刺带来的种种问题,及时且有效的去除毛刺是至关重要的。随着科技的进步,工业界已经发展出了一系列去除毛刺的方法。下面将介绍几种常见的去除毛刺的方法以及相应的预防措施。
1.手工去毛刺
手工去毛刺是最简单直接的去除方法,适用于较小批量或者对精度要求较低的工件。常见的手工工具包括锉刀、刮刀、砂纸、钢丝刷等。操作时,工人根据毛刺的位置和形状,使用不同的工具进行打磨、刮除。
手工去毛刺的优点是灵活方便,成本较低,但缺点是效率较低,且容易造成二次损伤。因此,适用于不要求高精度和批量生产的场合。
2.振动去毛刺
振动去毛刺是一种常见的批量生产方法,适用于大规模的零件处理。在这一过程中,工件和磨料一起放入振动机中,通过振动的作用,使磨料与工件表面产生摩擦,从而去除毛刺。这种方法适用于大批量的零件,能够在短时间内有效去除毛刺。
振动去毛刺的优点是效率高、成本相对较低,但需要根据工件的材质、形状等进行精细的调节,以避免损坏工件。
3.喷砂去毛刺
喷砂去毛刺是通过将砂粒高速喷射到工件表面,从而利用砂粒的冲击力去除毛刺的一种方法。这种方法适用于表面粗糙度较高或形状复杂的工件,能够在不影响工件结构的前提下,去除毛刺。
喷砂去毛刺适用于多种金属材料,尤其是硬度较高的金属,其优点是去毛刺效果好,适合大批量生产,但操作时需要注意安全防护,避免砂粒溅射造成伤害。
4.激光去毛刺
激光去毛刺是一种现代化的去毛刺技术,适用于高精度的加工要求。通过激光束照射工件表面,激光的高温能迅速熔化毛刺,从而实现去除。这种方法具有非常高的精度,且对工件表面损伤小。
激光去毛刺的优点是精度高、效率快,适合复杂形状和高精度要求的工件,但设备成本较高,需要较大的投资。
5.化学去毛刺
化学去毛刺是通过化学溶液对工件表面进行腐蚀,从而去除毛刺的方法。常用的化学溶液包括酸性溶液或碱性溶液。这种方法适用于形状复杂、精度要求较高的工件,能够在不损伤工件本体的前提下,去除细小的毛刺。
化学去毛刺的优点是适用于复杂形状的工件,但需要严格控制溶液的浓度和浸泡时间,以避免腐蚀过度,影响工件质量。
6.预防毛刺的方法
除了通过去毛刺工艺去除毛刺外,预防毛刺的产生也是降低生产成本和提高产品质量的重要措施。预防毛刺的方法主要包括:
优化加工工艺:在加工过程中,合理选择刀具、调整加工参数、提高设备精度等,可以减少毛刺的产生。
提高操作精度:操作人员的技能水平对毛刺的产生有很大影响。定期培训操作人员,提高其技能和操作规范,可以有效减少毛刺的发生。
使用优质刀具:优质的刀具能够减少磨损,提高切削效率,从而降低毛刺的产生。
改进模具设计:在冲压和铸造等工艺中,模具的设计直接影响毛刺的产生。通过优化模具设计,可以有效预防毛刺的形成。
总结
毛刺作为金属加工中的常见问题,对产品质量、安全性以及生产成本有着深远的影响。了解毛刺的成因和危害,以及掌握去除毛刺的技术手段,对于提升生产效率、降低生产成本、提高产品质量至关重要。通过合理的工艺设计、优化加工方式及采用先进的去毛刺技术,企业可以更好地应对毛刺问题,实现生产流程的优化与产品质量的提升。