化学去毛刺——提升制造品质的新技术
在现代制造业中,产品的精度和质量始终是企业竞争的关键。毛刺作为加工过程中不可避免的副产物,往往成为影响产品质量和性能的重要因素。尤其是在精密机械、汽车、电子等领域,毛刺问题更加显著。传统的去毛刺方法,如人工打磨、机械去毛刺等,不仅效率低,而且往往会造成二次污染,甚至影响产品的精度和外观。
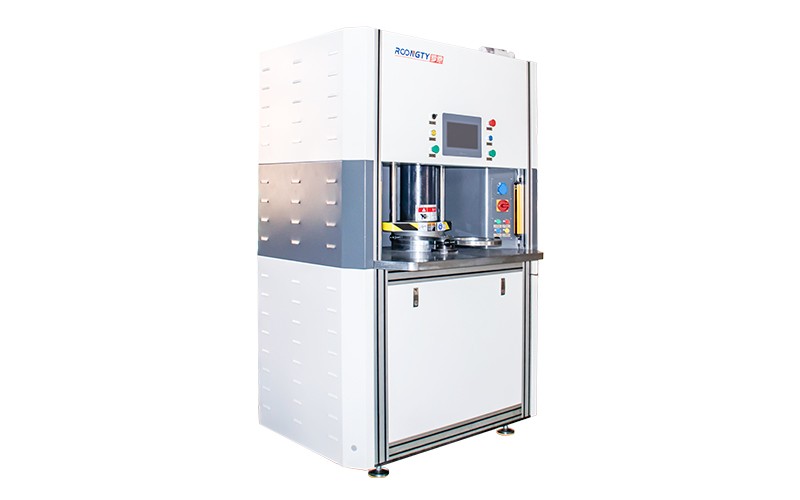
因此,随着科技的进步和环保理念的深入人心,化学去毛刺技术应运而生,并迅速在各大行业中取得了广泛应用。化学去毛刺,顾名思义,就是通过化学反应去除金属或合金表面的毛刺,这一技术具有很多传统去毛刺方法无法比拟的优点。我们将详细探讨化学去毛刺的工作原理、优势以及在各行业中的应用前景。
一、化学去毛刺的工作原理
化学去毛刺技术的核心原理是利用化学溶液与工件表面材料发生反应,选择性地去除毛刺部分,而不影响工件的主体部分。这一过程通常是在特定的化学环境下进行,通常通过浸泡、喷淋、涂覆等方式使化学溶液与工件表面接触。
常见的化学去毛刺溶液包括酸性溶液、碱性溶液以及一些特殊的中性溶液。在这些溶液的作用下,毛刺部分由于其微小的结构和特殊的化学性质,通常会比工件主体更容易被溶解,从而实现去除。
例如,酸性溶液能够腐蚀毛刺部分,而不会对工件主体产生过多的影响。因为毛刺表面的金属通常比工件主体的金属微观结构更加松散,化学溶液对其的侵蚀速度也会相对较快。而对于某些特殊的金属和合金,可能还需要特殊的化学溶液或添加剂,以确保去毛刺效果的避免对工件本身造成损伤。
二、化学去毛刺的优势
高效性
化学去毛刺相较于传统的机械去毛刺,不仅效率更高,而且能够实现批量处理。通过浸泡或喷淋等方式,可以同时处理大量工件,极大地提高了生产效率。化学去毛刺的处理时间相对较短,不会导致生产流程的长时间中断。
精准性
化学去毛刺能够精确地去除工件表面微小的毛刺,避免了传统机械去毛刺可能导致的误差或工件损伤。特别是在微小零件的去毛刺中,化学去毛刺展现出其无与伦比的精准性,不会改变工件的尺寸和结构。
环保性
传统去毛刺方法中,往往需要使用大量的金属磨料或其他化学物质,这些往往会产生废物,给环境带来负担。而化学去毛刺技术通常使用可回收的化学溶液,不仅减少了废物的产生,还能够降低生产过程中的噪音和粉尘污染,符合现代制造业的环保要求。
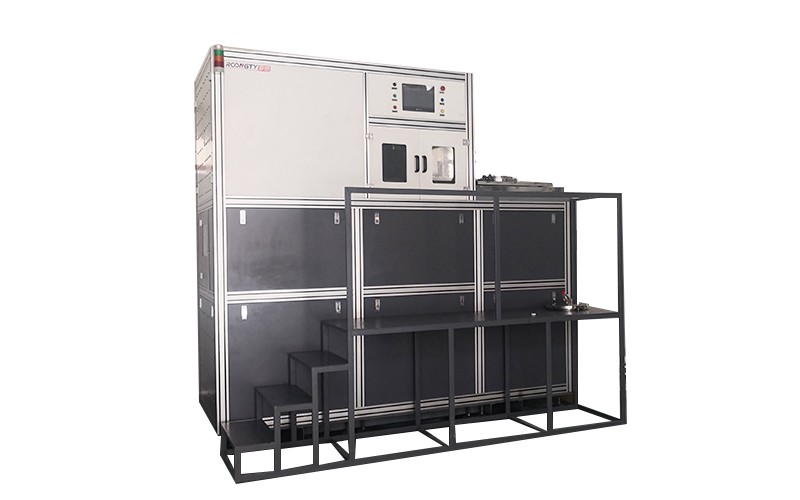
适应性强
化学去毛刺技术适用于各种金属材料的去毛刺,包括钢铁、铝合金、铜合金等。这使得该技术在多个行业中都能得到应用,特别是在航空航天、汽车、电子制造等高精度要求的领域。
成本优势
尽管化学去毛刺初期可能需要一定的设备投入和化学溶液的采购,但随着生产规模的扩大,化学去毛刺的单位成本将大幅下降。减少了人工操作和机械设备的磨损,能够在长期内降低企业的生产成本。
三、化学去毛刺的应用前景
随着科技的发展,化学去毛刺技术在制造业中的应用范围不断扩大。在精密加工、航空航天、电子工业等高端领域,化学去毛刺技术已经成为保证产品质量和生产效率的重要手段。未来,随着制造工艺的不断精进,化学去毛刺技术有望在更多行业中得到广泛应用,成为提升制造品质的必备工具。
四、化学去毛刺在各行业中的应用
精密机械制造
在精密机械制造中,毛刺不仅影响外观,还可能导致零件的配合不良、运转不顺等问题,影响产品的性能和使用寿命。化学去毛刺能够高效、精准地去除微小毛刺,避免了传统方法中可能存在的人工误差,确保了零件的精度和稳定性。
汽车行业
汽车制造中的零部件,如发动机、变速器等,对去毛刺要求非常高。毛刺如果没有及时去除,可能会导致零件卡死、磨损加剧,甚至危及行车安全。化学去毛刺技术凭借其高效性和精准性,广泛应用于汽车零部件的去毛刺工作,提升了产品的质量和可靠性。
电子产业
电子产品中的精密零件对毛刺的要求极为严格,尤其是在电路板的生产过程中,微小的毛刺可能会导致短路或电气故障。化学去毛刺技术能够在不损伤电路板表面的前提下,去除所有的毛刺,确保电子产品的稳定性和安全性。
航空航天
在航空航天领域,对零部件的精度要求极为苛刻,任何微小的毛刺都可能影响飞行器的性能。化学去毛刺技术在这一领域的应用,能够确保零部件的质量和精度,避免因毛刺问题导致的性能问题或安全隐患。
医疗器械
医疗器械的制造对精度要求极高,毛刺可能影响器械的功能,甚至危及患者的安全。化学去毛刺技术能够在不影响器械功能的前提下,高效、精准地去除毛刺,确保器械的安全性和可靠性。
五、总结
化学去毛刺技术凭借其高效、精准、环保的特点,正在逐步取代传统的去毛刺方法,成为现代制造业的重要技术手段。它不仅能够提升产品质量,减少生产中的误差,还能够降低成本、提升生产效率。未来,随着技术的不断发展和创新,化学去毛刺将在更多领域中发挥重要作用,成为制造业中不可或缺的一环。