毛刺与内径加工:如何实现精准的工艺控制与质量提升
在现代机械加工过程中,毛刺和内径问题是所有精密制造工作者无法忽视的关键因素。毛刺,是指在机械加工中,由于刀具切削力、材料受力不均或加工方式问题,导致金属或其他材料表面出现的一种不规则凸起。虽然毛刺看似是加工过程中的微小瑕疵,但它却会对产品的质量、功能甚至安全性造成严重影响。特别是在内径加工领域,毛刺的存在尤为突出,且往往影响到产品的配合精度与使用性能。
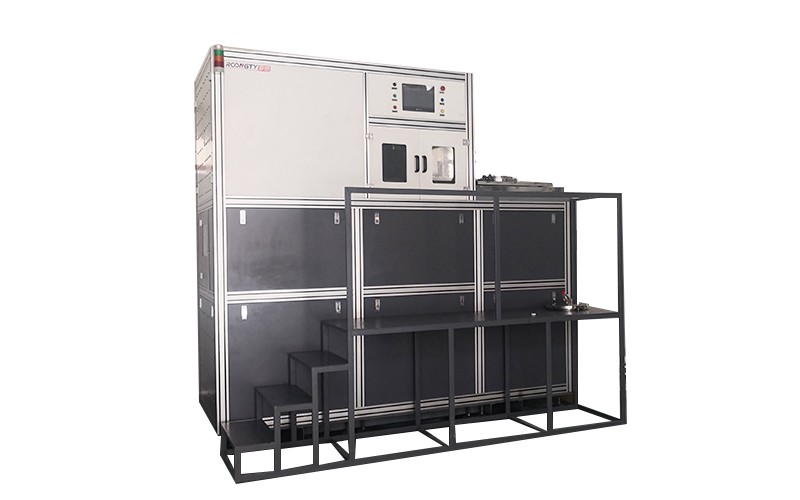
毛刺的产生原因主要有三个方面:一是刀具的磨损,二是切削参数的选择不当,三是工件材料本身的特性。例如,在内径加工过程中,刀具无法完全去除内壁的材料,造成毛刺的积累。尤其是内径较小或形状复杂的工件,毛刺问题更加突出。通过有效的工艺优化与设备升级,我们能够有效减少毛刺的产生,提高产品加工精度。
除了毛刺,内径加工的难点还在于如何确保内径的精准控制。内径加工的过程通常涉及到钻孔、镗削、铣削等操作,这些操作中每一项细节都对最终的内径精度有着重要影响。特别是在要求高精度配合的应用中,如精密轴承、汽车发动机零件等,任何微小的误差都会导致产品性能的下降,甚至失效。内径加工的难点在于如何确保加工过程中始终保持稳定的切削力和温度,避免出现加工偏差。
针对毛刺和内径加工的挑战,许多企业开始采用先进的加工技术和智能设备来提升加工精度。采用数控机床和高精度刀具可以有效提高加工精度,并减少毛刺的产生。数控机床通过精准的控制系统,能够在加工过程中实时调整刀具路径和切削参数,确保每次加工的稳定性,从而提高产品质量。
采用智能检测系统也是解决毛刺和内径精度问题的重要手段。通过集成传感器和测量系统,能够对加工过程进行实时监控,及时发现毛刺和内径加工误差,确保加工过程中的每个环节都在可控范围内。智能检测系统不仅能够提高生产效率,还能够减少人为操作误差,实现全程自动化控制。
在提升内径加工精度和控制毛刺的过程中,优化工艺也是一项至关重要的工作。传统的加工工艺往往难以兼顾加工精度和生产效率,因此许多企业开始寻求新的工艺方法,以实现更高的生产要求。比如,采用冷却液润滑技术可以有效降低切削温度,减小刀具与工件之间的摩擦力,从而减少毛刺的生成。通过合理设计切削路径和进给量,可以优化刀具的工作状态,减少加工误差。
除了工艺优化,材料选择对毛刺和内径加工的质量也起着决定性作用。不同材料的加工特性不同,硬度、韧性和耐磨性等都可能影响到毛刺的产生。因此,在选择材料时,除了考虑材料本身的性能要求外,还应综合考虑其加工性。对于某些难加工的材料,使用专用的刀具或调整加工参数,可以在最大程度上减少毛刺问题,并提高内径加工的精度。
除了传统的机械加工方法,现在一些新兴的技术也为内径加工提供了新的解决方案。例如,激光加工和电火花加工等技术可以在不接触工件的情况下精确切削,尤其适用于内径精度要求极高的工件。这些技术的应用不仅大大提高了加工效率,还有效避免了由于传统加工方法引起的毛刺问题。
在质量控制方面,现代化的质量检测技术和工具也为毛刺和内径加工提供了强有力的支持。通过采用激光测量仪、三坐标测量机等先进检测设备,能够对每个加工环节进行精确的检测和调整。这些高精度的测量工具可以及时发现加工误差并进行修正,确保每一件产品都能达到严格的质量标准。
毛刺和内径加工是现代精密制造中的两个关键挑战,但通过不断优化工艺、提升技术手段和智能化设备的应用,我们可以有效地解决这些问题,提高加工精度和产品质量。随着制造业技术的不断进步,我们有理由相信,未来的机械加工将更加精确、高效,并为各行各业提供更高质量的产品。