电解抛光配比:完美提升金属表面光洁度的秘诀
在现代制造业中,金属表面处理已经成为提高材料性能、增强耐腐蚀性及美观度的重要环节。而电解抛光作为一种高效、环保的表面处理工艺,因其优异的表面光洁度和提高耐腐蚀性的效果,得到了广泛应用。尤其在不锈钢、铝合金等金属材料的处理上,电解抛光更是成为了许多领域中不可或缺的技术之一。
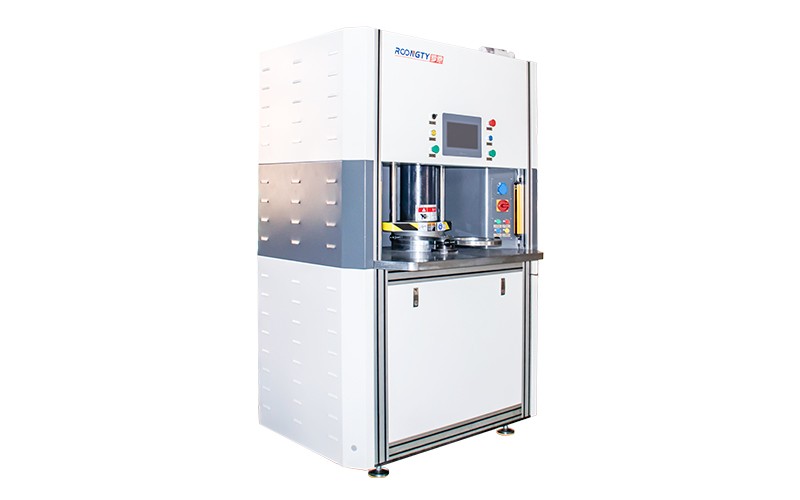
要达到理想的抛光效果,仅仅依赖抛光设备和技术是不够的。电解抛光的效果直接与配比的精细程度密切相关,这也正是许多从事表面处理行业的专业人员非常关注的问题。电解抛光配比是指在电解抛光过程中,电解液的组成成分、温度、电流密度等参数的配置。不同的配比将直接影响到金属表面抛光后的质量、光泽度、耐腐蚀性等多个方面。
电解抛光的基本原理
电解抛光作为一种特殊的表面处理方法,其原理是在金属工件表面通过电解液的电化学作用,去除金属表面微小的不规则凸起,从而使表面变得平滑并提高其光洁度。与传统的机械抛光不同,电解抛光并不需要使用机械力,而是通过电解液中的化学成分在电流的作用下,进行化学反应和溶解。
在电解抛光过程中,金属表面由于受到电流的影响,表面较高的凸起部分会比低凹部分先溶解,从而达到平整、光滑的效果。其最大的优势就是可以在不破坏金属表面材料的情况下,通过去除表面微小的不规则部分,显著提高其光洁度。
电解抛光配比的重要性
电解抛光的效果不仅仅与设备和操作技术相关,配比也是一个至关重要的因素。合理的配比可以让金属表面在最短时间内获得理想的光泽度和耐腐蚀性,过高或过低的浓度都会影响电解抛光的效果。以下是电解抛光配比的几个关键要素:
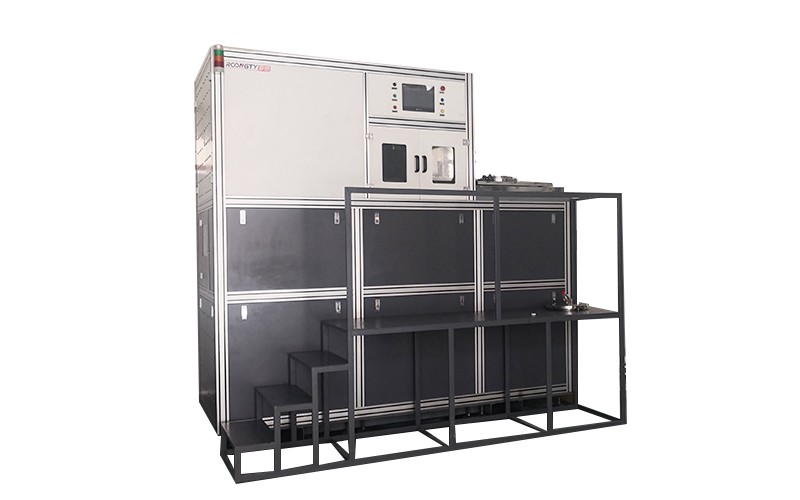
电解液的组成
电解液的组成直接影响到电解反应的进行。常见的电解液成分包括硫酸、磷酸、氟化物等。不同的金属材料需要根据其特性调整电解液的配比。例如,在处理不锈钢时,通常使用硫酸与磷酸的混合液,而在处理铝合金时,可能需要添加一定比例的氟化物以保证较好的抛光效果。
温度的控制
电解抛光过程中的温度是一个非常关键的因素。通常,较高的温度有助于加速金属表面的溶解速度,但温度过高也可能导致金属表面产生腐蚀或变色。因此,温度的控制需要与电解液的浓度和电流密度相匹配,以保证最佳的抛光效果。
电流密度与电压的调整
电流密度和电压是影响电解抛光效果的主要参数。电流密度过高,可能会导致金属表面出现过度溶解,甚至产生损伤;而电流密度过低,则可能导致抛光效果不明显。因此,在电解抛光过程中,需要根据不同的金属材料和工件的表面状态,精确调整电流密度和电压,以确保均匀抛光。
时间的控制
电解抛光的时间也是影响抛光效果的一个重要因素。抛光时间过长,金属表面可能会出现过度腐蚀,导致表面光泽度降低;时间过短,又可能达不到理想的光洁效果。通常,合理控制时间和其他配比参数的结合,能够确保最佳的表面光泽和均匀度。
不同金属的电解抛光配比
电解抛光的配比并不是固定的,不同金属材料在电解抛光过程中所需的配比也是不同的。下面我们将分别介绍不锈钢和铝合金的电解抛光配比。
不锈钢的电解抛光配比
不锈钢是一种常见的耐腐蚀性金属,广泛应用于医疗器械、食品加工设备、化学工业等领域。在不锈钢的电解抛光过程中,常用的电解液成分是硫酸和磷酸的混合液,比例通常为:硫酸:磷酸=3:1至5:1。硫酸有助于金属的溶解,磷酸则能增强金属的光泽度和耐腐蚀性。
对于温度,通常控制在50℃至70℃之间,电流密度一般保持在10A/dm²至20A/dm²的范围内,电压控制在10V至20V之间,时间控制在5至15分钟之间。通过合理的配比,可以获得理想的不锈钢表面光泽和耐腐蚀性。
铝合金的电解抛光配比
铝合金因其轻便、高强度、耐腐蚀的特点,广泛应用于航空、汽车、电子等领域。铝合金的电解抛光配比与不锈钢有所不同,常用的电解液成分是硫酸与氟化物的混合液,比例通常为:硫酸:氟化物=4:1至6:1。
铝合金的电解抛光对温度的要求较高,通常控制在70℃至90℃之间,电流密度为15A/dm²至25A/dm²,电压保持在15V至25V之间。抛光时间控制在3至10分钟之间。通过合理的配比,不仅能够提高铝合金的光泽度,还能提高其表面的耐腐蚀性能。